Labeling Methods
Our labeling and print-and-apply systems can use several distinct application methods with different kinds of applicator arms so that they can perfectly match with your products. It is possible to apply labels in different areas of your products, no matter if they are simple boxes, bottles, cylindrical objects or have irregular shapes. You can even opt to apply two or three labels in the same product with a single system. Know more about each kind of application method and application zones below.
Wipe-On
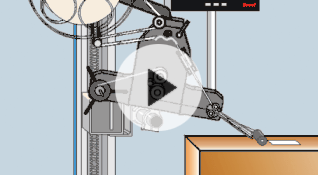
- Does not Require Compressed-Air
- Product Stoppage is not Needed
- Less Movable Parts and Energetic Consumption
- Extremely Economic Method
- Side, Top or Bottom Applications
- Short Cycling Times
In this method, the label advances at the same speed of the product traveling on the conveyor and goes along with the product's surface. The label is then softly pressed against the product by means of a soft roll or brush. The great advantage of this method and what makes it so popular is the fact that there is no need for compressed air and the fact of being extremely economical. And since there are no movable parts, the wearing down of the system and the maintenance are minimal. The machine can apply labels on the sides, tops or bottoms of the products. Because no time is lost moving a tamp applicator, the cycling times are very short.
Tamp-Blow (Linear)
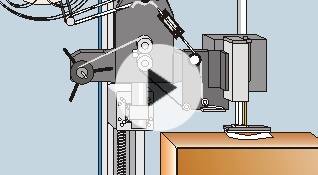
- No Contact with the Products
- Product Stoppage is not Needed
- Application in Products with Variable Heights (requires proximity sensor on the tamp)
- Side or Top Applications
- Application is Independent of the Speed of the Production Line
- Less Impacts and Mechanical Wear
- Usually, it can also work in Blow-On or Tamp-On modes
Here we have a tamp that receives the label and holds it by means of air suction. Then it gets closer to the product, where it inverts the air flow to blow the label into the surface. The system can apply labels on the side or on the top of the product. The advantage of this method is that there is no contact at all with the product and, with a proximity sensor installed on the tamp pad, it is possible to apply labels on top of products that have variable heights, without having to adjust anything. The tamp can wait for the product before advancing or extend immediately and wait for the product while it is already down, being the latter option called Inverted Tamp-Blow. Because there are no impacts against the products, the system wear is very low. It can be easily configured to work in Blow-On mode and, if the tamp is equipped with springs, it can also work in Tamp-On mode.
Tamp-On (Linear)
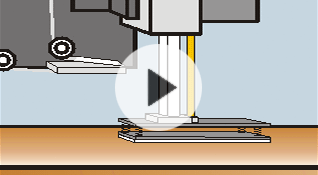
- The Tamp Presses the Label for Better Adhesion
- Side or Top Applications
- Usually, it can also work in Blow-On or Tamp-Blow modes
It is almost identical to the Tamp-Blow method, with the difference that the tamp is a special spring tamp, so that we can have a light contact with the products, pressing the label firmly onto the product's surface, usually not requiring additional pressure rolls. Ideal for surfaces where the labels do not stick so well. Requires product stoppage, however, it can easily be configured to work in Blow-On or Tamp-Blow modes.
Blow-On (Linear)
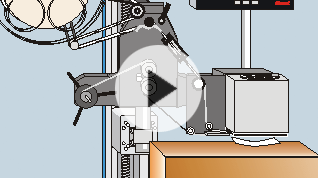
- No Contact with the Products
- Product Stoppage is not Needed
- Top Application
- Application is Independent of the Speed of the Production Line
- Less Impacts and Mechanical Wear
- Short Cycling Times
- Economical Method
In this method, the label is applied using air blow, but from a fixed position, where there is no tamp (or when it exists, the tamp does not move from its position). When the system is equipped with an applicator arm with tamp, it can also be configured to work in Tamp-Blow or Tamp-On modes, but to reduce costs usually the system only brings an air grid also known as Blow-Box.
Tamp-Swing (Tamp-Blow Front/Rear)
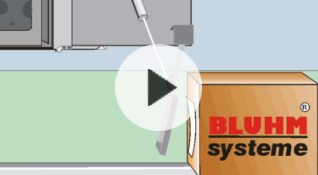
- No Contact with the Products
- Product Stoppage is not Needed
- Front and/or Rear Applications
- Top or Side Application in Blow-On mode
- Double Application
- Application is Independent of the Speed of the Production Line
- Less Impacts and Mechanical Wear
- Usually, it can also work in Tamp-On and Blow-On
Here we have a swinging tamp, which allows the application of labels onto the product's frontal or rear sides. After the rotational movement is executed, it is basically a normal Tamp-Blow that blows the label onto the product's surface without contact, but it can work in Tamp-On with contact as well. The system can apply in the frontal or rear part of the product and it can even apply a second label on the top or side, without any arm movement (Blow-On mode) or by doing a very small movement.
Twin-Tamp (Tamp-Swing + Linear)
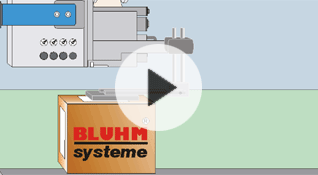
- No Contact with the Products
- Product Stoppage is not Needed
- Front and/or Rear Applications in Swing mode
- Top or Side Applications in Tamp-Blow mode
- Double Application
- Application in Products with Variable Heights (requires proximity sensor on the tamp)
- Application is Independent of the Speed of the Production Line
- Less Impacts and Mechanical Wear
- Usually, it can also work in Tamp-On and Blow-On
This method is similar to the Tamp-Swing, but besides the rotative movement, the tamp can also do a liner movement, extending forward just like in the Tamp-Blow method. Basically, it is the combination of both methods to apply labels in two adjacent sides of the same product, either front/rear plus side or front/rear plus top, allowing variable heights.
Corner-Wrap
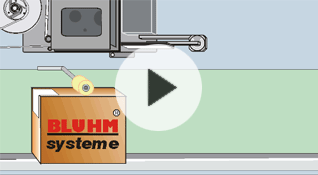
- Application Along the Corners of the Products
- Product Stoppage is not Needed
- Edge Between the Front and Side
- Edge Between the Front and Top
- Also for the Rear Edges (requires split-tamp and stoppages or low speeds)
This method allows the application of labels around a corner of a box. In the initial phase the label is partially applied on the front or rear of the product, leaving part of the label protruding out of the edge. Then, there are several ways to make the label go around the corner. One way is having the extended tamp waiting for the impact, pressing the remaining portion of the label against the side or top of the product as it retracts back. Another way is to use a pressure roll or brush downstream the production line. Lastly, an extendable pressure brush can be attached to the tamp itself or even a double tamp, normally called "Split-Tamp", can be used.
Wrap-Around (Wipe-On)
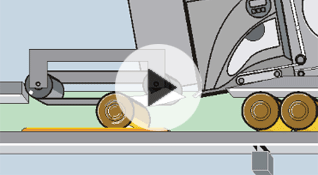
- Does not Require Compressed-Air
- Product Stoppage is not Needed
- Less Movable Parts and Energetic Consumption
- Extremely Economic Method
- Applications Around Cylindrical Products
- Short Cycling Times
This method is a special case of the Wipe-on method, in which the labels are applied around bottles, flasks, cans and other cylindrical products.
Tires, Cans and Other Cylindrical Products (Wrap-Around for heavy products)
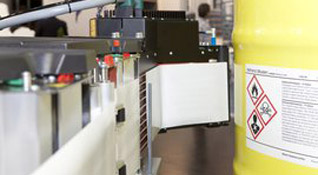
- Applications on Cylindrical Products
- Product Stoppage is not Needed
- Does not Require Compressed-Air
- Application is Independent of the Speed of the Production Line
- Short Cycling Times
An extremely innovative method that produces amazing results. And the best is that the tamp is 100% electric without the need of compressed air. This is achieved because there are electrical fans generating the suction to hold the label and the cords make the label travel to the extremity of the tamp.
Pallet Applicators
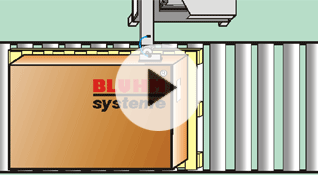
- Reinforced and Longer Arms for Pallet Application
- Application up to 3 sides with a 3-axes arm
- Application on 1 or 2 sides without Stoppages
- With or Without Contact Against the Pallet
- Less Impacts and Mechanical Wear
The applicators designed for pallets have a longer and sturdier special arm, which is usually capable of performing movements along three axes, to apply labels on three sides of the same pallet. The application can work in Tamp-On or Tamp-Blow modes. For one- or two-sided applications, a stop may not be required as long as the pallets travel at speeds that allows time for the labels to be printed.
Optional Rejection Tamp
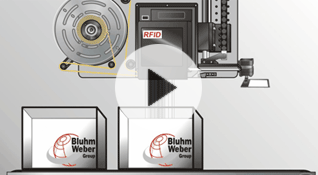
- Prevents Unreadable Labels from being Applied
- Works for Barcodes or RFID
- Automatic Reprints after a Rejection (requires stoppage)
- Switches to Error after Reaching Configurable Number of Retries
An optional tamp pad that, in case of detection of a bad reading of a barcode or RFID label, advances to intercept the defective label before it is applied onto the product. If there is stoppage of the production line, a reprint can be performed automatically. In case of consecutive bad readings (and the number of tries is configurable), the system will enter in error status.
Geset Complete Lines
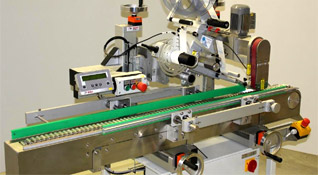
- Includes Conveyor Belt
- Includes Adjustable Product Guides
- Includes Labeling or Print-and-Apply Systems
- With Cranks to Adjust Positions
Complete systems that include a small conveyor belt with special alignment guides to perfectly apply labels in flasks or other containers with more complex shapes.
Customized Systems
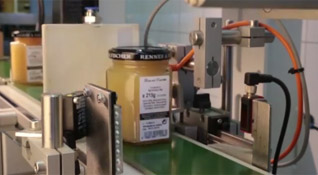
- For Specific Shape and Type of Product
- For Specific Shape and Type of Label
- Custom-Made
You have a product and/or a label with a difficult shape? We accept
the challenge! We have lines for many types of products and
applications.
Contact us right now!
Most Common Applications
Single Applications
-
Side
-
Top
-
Bottom
-
Front
-
Rear
-
Side (Flat Bottles)
-
Top (Lids)
Double Applications
-
Front + Side
-
Side + Rear
-
Front + Top
-
Top + Rear
-
Front + Rear
Triple Applications (Pallet Applicators)
-
Front + Side + Rear
Corner Applications
-
Front + Side
Edge -
Side + Rear
Edge -
Side + Top
Edge -
Front + Top
Edge -
Top + Rear
Edge -
2 Edges
-
4 Edges
Wrap-Around Applications
-
Wrap-Around
-
Wrap-Around (Double)
-
Wrap-Around (Conical)
-
Tube Interiors